サンアントニオ・スパーズ
<ウェブサイト名>
<現在の時刻>
お問い合わせ 会社情報 製品・サービス 研究開発 サステナビリティ 採用情報 ニュース ホーム 研究開発 JX金属のコア技術 創業以来100年以上にわたって培ってきた、当社の競争力の源泉であるコア技術を紹介します。今後、これらの技術をさらに進化・発展させると共に、外部パートナーとのコラボレーションを推進、社会に新しい価値を提供していきます。 × 高純度化 高純度化|各種精製、溶解技術を駆使して、不純物の低減を実現 高純度化-各種精製、溶解技術を駆使して、不純物の低減を実現 精製 溶解 精製 配線幅がナノメートルレベルと微細化が進む半導体デバイス向けをはじめ、先端の電子部品に使われる金属材料には高純度化が求められています。当社は各種金属原料に対応した独自の社内精製プロセスを保有、これにより、金属の本来の特性を発現する高純度金属や、それらを原料とするスパッタリングターゲットなどの業界最高レベルの高純度材料を提供しています。 精製技術の例 溶融塩電解装置 水溶液中で電気分解することが難しい金属元素は、溶融塩電解という方法で精製し、高純度化することが可能です。 適用製品例 9N Cu 世界最高レベルの高純度 9N(99.9999999%)を実現。高純度化することで、その金属本来の特性を発現します。 溶解 金属の高純度化には溶解プロセスが欠かせません。金属には各々固有の融点があり、それぞれに対応した溶解技術が必要になることに加え、雰囲気や炉体からのコンタミネーションも防ぐ必要があります。当社では多様な金属原料を幅広い用途に適用していることから、その用途に応じた各種溶解技術を保有しています。自社製品に用いる原料の高純度化から、市場に提供する各種高純度金属の製造まで、幅広く活用しています。 溶解技術の例 各種溶解設備 真空誘導溶解炉、電子ビーム溶解炉、プラズマアーク溶解炉など様々な炉を保有し、元素に応じた適切な溶解ができます。 適用製品例 スパッタリングターゲット(Ta) 溶解プロセスにより、業界標準を大きく上回る、純度5N5(99.9995%)のスパッタリングターゲットのご提供が可能です。 × 組成・組織制御 組成・組織制御|結晶レベルでの制御により、素材の高機能化を実現する 組成・組織制御-結晶レベルでの制御により、素材の高機能化を実現する 金属・合金材料の制御 セラミックス材料の制御 単結晶育成 金属・合金材料の制御 最先端の金属材料では、その組成や純度のみならず、結晶粒の大きさや結晶方位が特性や品質に影響します。また、これらは必ずしも結晶粒が小さい方が良い、結晶方位が揃っている方が良い、というものではなく、その用途によって求められる状態が異なります。当社では、長年蓄積した製造ノウハウやシミュレーション技術に基づき、合金組成や結晶状態の検討を行い、独自の加工プロセスや熱処理プロセスの組合せにより、必要な特性を実現しています。 金属・合金材料の制御技術の例 合金材料の組織制御 合金は圧延と熱処理を繰り返すことで製造されますが、加工や熱処理等の条件を最適化することで、製品の結晶粒径や配向を制御・管理します。 適用製品例 FPC用圧延銅箔(HA,HA-V2) 折り曲げ可能なフレキシブル基板には、その配線用銅箔にも屈曲性が求められます。結晶粒を大きく、かつ方位を揃えることで、折り曲げても破断しにくい銅箔となっています。 セラミックス材料の制御 透明導電膜用のITO(In-Tin-Oxide)スパッタリングターゲットなど、各種のセラミックス材料の製造において、その原料から内製を行い、粒径レベルでの制御を行っています。その後、高圧焼結など、材料に合わせたプロセスを適用し、高密度かつ高品質のセラミックス材料を提供しています。 セラミックス材料の制御技術の例 ホットプレス 真空または不活性雰囲気下での高温焼結が可能な装置です。当社では試験用から製造用まで様々なサイズのホットプレス装置を保有しており、ご要望のサイズに応じた装置の選定が可能です。 適用製品例 ロータリーIGZOターゲット IGZO(In-Ga-Zn-Oxide)はスマートフォンなどのディスプレイ用の透明半導体に用いられます。当社ではお客様の装置環境に合わせ、板状(プレーナー)、円筒状(ロータリー)ともに提供しています。 単結晶育成 当社では融液成長法により、化合物半導体の単結晶を製造しています。単結晶育成方法にはいくつかの方法がありますが、化合物半導体結晶に適した製造方法を選択し、結晶育成時の温度プロファイルなどの育成条件の最適化により、大口径かつ、結晶欠陥が少なく、ドーパントの濃度分布の均一な化合物半導体インゴットを製造し、高品質の化合物半導体基板を提供しています。その代表製品であるInPでは、その高品質が認められ、光通信などIoT時代を支える用途において、高いシェアを獲得しています。 単結晶育成技術の例 LEC(Liquid Encapsulated Czochralski)法 融液上部に種結晶を接触させ、回転させながらゆっくり引上げる単結晶育成方法です。融液表面を液体で封止し、蒸発による組成変化を防ぎます。 適用製品例 CdZnTe単結晶基板 赤外線や放射線の検出器用途に検討されている化合物半導体基板。世界最大級のサイズとともに、添加物であるZnの均一な面内濃度分布など、高い品質を誇ります。 × 粉体制御 粉体制御|粒径などを制御した各種金属・セラミックス粉の実現 粉体制御-粒径などを制御した各種金属・セラミックス粉の実現 粉体の製造 粉体の取り扱い 粉体の製造 自社製品の原料から、市場に提供しているものまで、多様な粉体を製造しており、その範囲は合金、塩化物、酸化物など、多岐にわたっています。また、その用途も金属3Dプリンターから、粉末冶金技術により製造されるスパッタリングターゲットの原料粉まで、広範囲に及んでいます。当社では、湿式法や乾式法などの各々の材料に適した粉体製造技術を有し、更に造粒による粒径の制御や、表面処理による特殊機能の実現など、粉体の高機能化へのニーズにも対応しております。 粉体の製造技術の例 ガスアトマイザーやジェットミル等粉末製造に必要な各種装置を有しており、目的の品質に応じたプロセスの選定が可能です。 適用製品例 スパッタリングターゲット(W) 高度な粉体合成・粉砕プロセスにより、高純度(5N)かつ微細な組織を有するスパッタリングターゲットのご提供が可能です。 粉体の取り扱い 当社では金属・酸化物などの、様々な粒径や形状の粉体の取り扱いを行っております。これらの粉体は、その粒径や粒度分布を、用途に応じてブロード、またはシャープに制御する必要があります。また、ナノメートルからサブミクロンメートルといった微小粒径の粉体を取り扱う場合、凝集などの課題への対応も必要となります。これらに対し、粉体の分散性の向上や造粒など、様々な粉体の取り扱いの技術を有しております。 粉体の取り扱い技術の例 粉砕・造粒・分級 ジェットミルは各種金属粉の粉砕や、分散性向上のために、様々な粉体の製造工程で用いられています。 適用製品例 電解銅粉 電解銅粉は、その樹枝状形状により、焼結性、圧縮性に優れており、粉末冶金製品の必須原料として、含油軸受、電気ブラシ、摩擦材などのほか、触媒用、塗料用などの各方面でも使用されています。 × 精密圧延・精密加工 精密圧延・精密加工|世界最薄の圧延銅箔から超微細形状の加工まで 精密圧延・精密加工-世界最薄の圧延銅箔から超微細形状の加工まで 圧延加工 バルク加工 圧延加工 当社が保有する圧延加工の技術は、世界で唯一、銅資源の開発から一貫して製造することができる圧延銅箔から、インゴットから製造されるスパッタリングターゲットまで、幅広い製品の製造に活用されています。圧延銅箔の製造においては、目標の厚さを実現するまで圧延工程を繰り返すため、1回の圧延における面内厚さのばらつきが、最終製品では大きなばらつきとなって現れます。当社では圧延機だけでなく、プロセス全体の改善に取り組んでおり、圧延銅箔においては世界で最も薄い5um厚の量産技術の確立に成功しました。 圧延加工技術の例 精密圧延 独自のノウハウを織り込んだ、カスタムメイドの圧延機と焼鈍プロセスまで含めた一貫工程管理により、極薄かつ平坦な圧延銅合金箔を製造しています。 適用製品例 チタン銅箔 銅合金の中でも固いチタン銅を圧延し、薄さ30umの箔を製造。その薄さのばらつきは±0.2um程度と、公差1%以下に抑えられています。 バルク加工 化合物半導体は単結晶のインゴットから、お客様からの要求に応じて、求められる厚さや平坦度を持った基板に加工して出荷されます。インゴットから基板に切り出す方法として、マルチワイヤーソーや内周刃による切断などがありますが、当社では生産効率の高いマルチワイヤーソーを採用しています。特に平坦度はお客様での最終プロセスにおける歩留まりに影響する為、その要求仕様を満たすことが重要です。この切断技術と合わせて、下流工程の研磨により、非常に平坦な化合物半導体基板を提供しています。 バルク加工技術の例 マルチワイヤーソー ワイヤーを高速駆動しながら砥粒を供給し、最小限の加工代でインゴットをウェハ状に切断します。 適用製品例 InP基板 フォトリソグラフィ工程で求められる露光精度に対応した、高平坦度基板をご提供します。 × 表面制御 表面制御|独自の表面制御技術による、素材の新たな価値の実現 表面制御-独自の表面制御技術による、素材の新たな価値の実現 研磨・エッチング・洗浄 成膜・めっき 表面処理 接着・接合・複合化 研磨・エッチング・洗浄 当社が提供するスパッタリングターゲットなどの材料は、その組成や純度だけでなく、表面状態もお客様のプロセスにおける製造効率に影響します。この為、出荷前の最終工程において、エッチングによる表面の粗化から鏡面仕上げまで、求められる特性に応じた最終加工を行っています。 研磨・エッチング・洗浄技術の例 CMP(化学的機械研磨) 研磨剤の化学作用に、研磨パッド・砥粒成分による機械作用を併せることで、被加工物を低欠陥、高精度に研磨します。 適用製品例 SR (スパッタレディ™) 製品表面を極限まで平坦にすることで、スパッタ時のアーキングなどの品質課題を低減しています。 成膜・めっき 当社では電解・無電解ともにめっきの技術を社内保有しており、そのいずれもミクロンレベルの高精度めっきが可能です。その技術は、銅箔と基板の密着性を向上する粗化処理から、金属部品への微細電解めっきや半導体ウェハへの無電解めっきの受託事業など、幅広く適用されています。 成膜・めっき技術の例 無電解めっき(UBM) UBM(Under Bump Metallurgy)とは、半導体ウェハのボンディングパッド部やはんだ接合部へのめっき加工です。当社は台湾と日本の2拠点にクリーンルームを保有、自社で開発した無電解めっきプロセスにより、顧客ニーズに合わせた受託加工サービスを行っています。 適用製品例 銅箔粗化処理:BHM処理 当社独自の粗化処理仕様により、基板との密着性を維持しながら、平坦性を向上することで、高周波信号の伝送損失低減を実現しました。さらに粗化処理に用いられる材料の改良により、エッチング性を向上させ、より微細な回路形成を可能としています。 表面処理 銅箔や金属粉の表面に用途に応じて様々な表面処理を行うことで、素材の機能を失うことなく必要な機能を付与することが可能となります。その表面処理によって、銅箔の酸化防止から、金属粉の焼結挙動の制御といったユニークな機能まで実現しています。 表面処理技術の例 金めっき封孔処理 金めっき膜の表面に約2nmの有機表面処理膜を形成することにより、腐食性ガス雰囲気においても孔腐食を防止することができます。 適用製品例 配線やコネクタ端子などの腐食防止により、良好な接続性を維持できるようになります。 接着・接合・複合化 各種スパッタリングターゲットはバッキングプレート(BP)やバッキングチューブと呼ばれる、スパッタリング装置に設置する為の台座に接合して出荷されます。このBPとスパッタリングターゲットとの接合状態が不均一な場合、スパッタリング時にターゲット表面の温度が不均一になり様々な障害が生じます。そこで、ろう材による接合や異種材料間の拡散接合など、それぞれの材料に適した技術により、均一で強固な接合を実現しています。また、異種材料接合技術の応用により、銅箔と樹脂の複合材など、新しい材料の開発を進めています。 接着・接合・複合化技術の例 ろう材ボンディング・拡散接合 ろう材ボンディングは材料問わず脆性材料であっても柔軟に接合することが可能です。拡散接合は材質に制限はあるものの、非常に高強度の接合が可能です。 適用製品例 スパッタリングターゲット 当社の半導体用スパッタリングターゲットはBPに接合して出荷されますが、その材料に応じ、ろう材接合品、拡散接合品、更にはBP一体型ターゲットのラインナップがあります。 × 分析・評価・解析 分析・評価・解析|高度な分析・評価技術により、高機能・高品質材料を実現 分析・評価・解析-高度な分析・評価技術により、高機能・高品質材料を実現 無機・有機分析 表面分析・構造解析 実使用環境評価 計算科学の活用 無機・有機分析 製品保証、原料評価、工程管理、環境保全から研究開発まで、分析技術は当社の事業活動に不可欠な基盤技術です。そのため当社では、最新の分析装置の導入はもちろん、分析技術の開発にも取り組んでいます。一例として高純度金属の開発や品質保証に対応するためGDMS(グロー放電質量分析装置)やICP-MS(誘導結合プラズマ質量分析計)の分析技術の深化を図っています。また、最新の分析技術の利用だけでなく、金銀の乾式試金分析のようなクラシカルではありますが、高精度、高正確性の分析技術も大切にしています。 無機・有機分析技術の例 GDMS及び検出下限の例 国内で、最も多くのGDMSを保有しています。各種不純物の含有量を測定、当社の高純度材料の開発を支えています。 ICP-MS/MS ICP-MSの中でも共存元素の妨害が少ない最新鋭のICP-MS/MSを導入しています。 乾式試金分析 乾式試金分析は、重量法をベースとした分析法で、高精度、高正確性が特徴です。大変な手間と時間を要する分析法ですが、独自の改良を加えつつ、現在も実施しています。 表面分析・構造解析 表面分析·構造解析では、SEM, STEM, MLA, XPS, AESなどの最新機器を用い、材料の観察·分析を行ないます。STEMでは、~1nmという超高分解能を生かして化合物半導体やスパッタ膜の構造を調査したり、高機能銅合金の機能発現機構を解明したりすることで製品の性能向上に貢献しています。また、化合物(鉱物)の同定能力向上にも取り組んでいます。MLAでは、樹脂に包埋した微小鉱物数万粒を一気に分析し、鉱石の平均的な鉱物組成を求めることで、資源開発·製錬効率の向上や、浸出プロセスの開発に貢献しています。 表面分析・構造解析技術の例 STEMによるOs蒸着膜の評価例 Si基板上に1nmレベルで形成したOs蒸着膜の分析例です。1nmという極薄膜でもSTEMで分析可能です。 MLAによる鉱石Aの平均組成解析例 MLAで鉱石を広範囲にわたって分析することで、鉱物の種類ごとの分布や平均組成の解析に成功しました。通常、数万粒の分析を一気に行います。 実使用環境評価 当社の製品は、材料としてお客様の製品に組み込まれて使用されます。当社ではお客様が使用される条件での評価を行うことで、その最終形態で期待される機能・特性を実現しています。 実使用環境評価技術の例 スパッタリング成膜評価 スパッタリングでは、ターゲットから飛び出した原子が基板に堆積し、薄い膜を形成します。当社内でスパッタリングを行い、その薄膜特性を確認することで、ターゲットの品質向上や性能改善を行っています。 FPC折り曲げ評価 FPC(フレキシブル基板)は、折り曲げて使用される為、回路形成に用いられる銅箔は折り曲げても破断しないことが重要です。当社では実際にFPCの状態で折り曲げ試験を実施、求められる十分な強度があることを確認しています 計算科学・情報科学の活用 当社ではシミュレーションやデータ解析の技術を保有、さらに外部企業や研究機関などとも連携することで、その技術の向上を図っています。この計算科学の技術を応用し、新しい合金組成の設計や、品質改善などに役立てています。 計算科学の活用例 熱力学解析による新規合金組成の探索 お客様のニーズに合わせて様々な先端素材を開発・製造しております。その合金設計においては熱力学解析ツールを用いて3元系、4元系以上の合金組成の網羅的探索を行い、確実な製品化や開発スピードの向上に役立てています。 情報科学の活用例 SVMを用いた製造プロセスの最適化 製造現場のスマートファクトリー化を進めており、得られた製造ビッグデータを決定木、ベイズ最適化、深層学習など様々な解析手法を用いて分析し、品質改善に役立てています。掲載の図はサポートベクターマシーン(SVM)を用いた製造プロセスの最適な条件の探索の例です。 × 分離・抽出 分離・抽出・精製|資源からリサイクルまで、持続可能な社会を支える 分離・抽出-資源の安定供給からリサイクルまで、サステナブルな社会を支える 資源開発 金属製錬 リサイクル 安全・浄化 資源開発 当社はロス・ペランブレス、エスコンディーダ、さらに日本資本100%のカセロネスなど、世界有数の銅鉱山に出資しています。権益銅生産量は年間約20万トン(2018年実績)を誇り、電線から電子部品まで、日々の生活に欠かせない、銅資源の安定供給に貢献しています。 資源領域における技術開発の例 JXヨウ素法 当社では、ヨウ素を用いた、低品位銅鉱石から効率的に銅を分離・回収する技術を開発しています。チリにおいてパイロット試験を実施、同プロセスの実用可能性と、銅浸出性能の向上効果を確認しました。現在、この成果を活用し、鉱山での実用化に向けて取り組んでいます。 資源開発拠点例 カセロネス鉱山 当社グループが主体となり、100%日本資本によるチリ・カセロネス銅鉱山の運営を行っています。同鉱山では、2013年からSX-EW法による銅地金の生産(3万トン/年)を、2014年から銅精鉱の生産(15万トン/年)を開始、生産期間は2040年までの28年間を予定しています。 金属製錬 当社は精鉱バーナー、溶媒抽出法を取入れた湿式精金銀プロセス等独自開発プロセスを多く有し、銅精鉱だけでなく、E-スクラップ等のリサイクル原料の処理、4N(純度99.99%)電気銅、貴金属、レアメアタル、硫酸等の安定供給により社会に貢献しています。また、排熱回収発電等、環境保全にも積極的に取組む世界トップクラスの銅製錬メーカーです。 銅製錬(乾式·湿式製錬)技術の例 Flash Smelting Furnace 精鉱バーナー 反応性に優れた精鉱バーナーを独自開発し、銅精鉱反応熱を利用しスクラップ原料処理をアップ、また、各工程排熱を回収し高効率発電を積極的に行い資源循環型社会に貢献したプロセスです。 貴金属回収工程銅電解スライム湿式処理 電解採取により4N電気銅を生産。また、生成した銅電解スライムを原料として、世界初の高効率な銅電解スライム湿式処理プロセス(溶媒抽出)を独自に開発し、貴金属・レアメタルを精製しています。 佐賀関製錬所全景 製錬所は、関サバ・アジ・ブリで有名な佐賀関半島(大分県)に位置します。その他、日立(茨城県)には当社発祥の地(「ある町の高い煙突」新田次郎著の舞台)となる事業所も健在であり、持続可能な社会の実現を企業理念としたDNAを受継いでいます。 リサイクル 金属製錬の技術を活用したプロセスにより、リサイクル原料から銅·貴金属·レアメタルなどを効率的に回収するとともに、産業廃棄物について二次廃棄物を出さないゼロエミッション型の無害化処理を行っています。日立事業所にHMC(Hitachi Metal-recycling Complex)製造部を設置し、多様な有価金属の回収を手掛けると同時に、リサイクラーや湿式メーカーとの集荷ネットワークの強化を図っています。 リサイクル技術の例 LiBリサイクル 車載LiBに含まれるレアメタルを、金属塩をはじめ、溶液、メタル等、顧客のニーズに合わせた様々な形で回収する技術を保有しています。 リサイクル拠点の例 JX金属サーキュラーソリューションズ LiBリサイクルのプラントスケールでの実証試験を行っており、民生用LiBからの金属回収技術を確立しています。2021年度からは、車載用LiBのクローズドループリサイクルの実証化に向けて、正極材原料として直接使用可能な高純度の金属塩を回収する実証試験を始めています。併せて、湿式金属回収に適したLiBの前処理技術の開発も実施しています。 安全・浄化 社会の一員である当社は、環境対策や従業員も含めた安全への取組がその事業活動における最優先の義務と考えています。その思想は創業の地である日立鉱山の煙害対策として建設された大煙突に始まり、100年以上もの間、脈々と受け継がれています。 安全・浄化技術の例 休廃止鉱山の坑廃水処理 坑内から湧き出る坑水と、堆積場などの鉱山施設から排出される廃水からなる坑廃水は、鉱山に残る鉱石などに雨水などが接触することによって発生します。この坑廃水は強酸性であり、環境への影響があることから、鉱山を休廃止した後も、1日も欠かさず処理を行う必要があります。 安全活動への先進技術導入 事業所における災害リスクへの対策として、先進技術を導入しています。一例として、重機と人との接触防止を目的に、磁界発生装置と作業者に装着するICタグの組み合わせによる重機自動停止装置を導入しました。障害物などの影響なく人を早期に検知して、重機を停止できます。 コア技術の組み合わせによる当社製品・事業展開の例 薄膜材料 タンタル・ニオブ 機能材料 金属・リサイクル 資源 ページ上部 会社情報 製品・サービス 研究開発 サステナビリティ 採用情報 ニュース プライバシーポリシー このサイトについて 電子広告 サイトマップ Copyright © JX Metals Corporation All Rights Reserved.
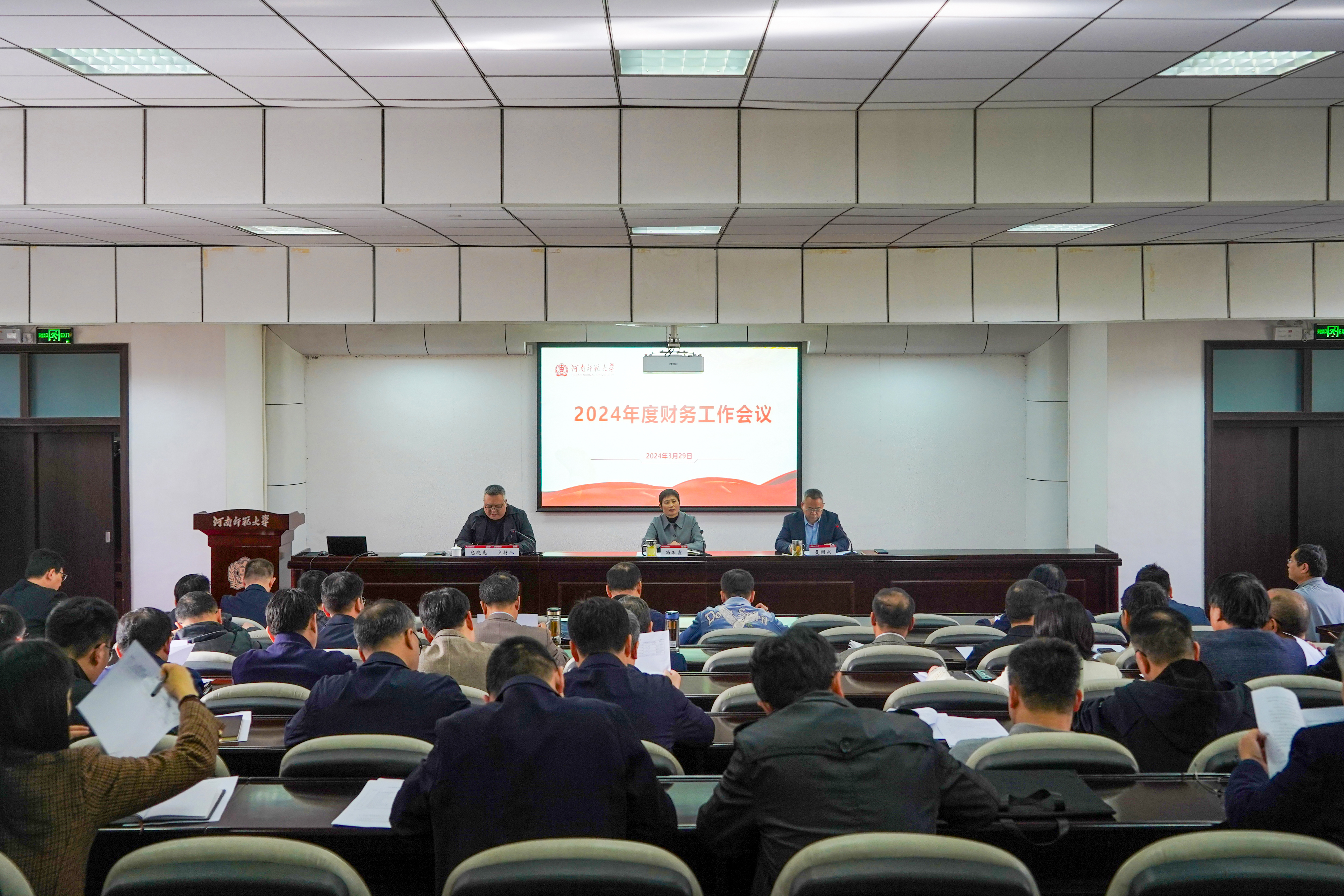